Some Known Details About Premier Aluminum Llc
Table of ContentsExcitement About Premier Aluminum LlcNot known Facts About Premier Aluminum LlcThe Ultimate Guide To Premier Aluminum LlcGetting My Premier Aluminum Llc To Work
(https://anotepad.com/note/read/4mnaxd4k)Traditionally, a buyer's primary duty was to discover certified and receptive providers. Sometimes, buyers assumed that any kind of supplier happy to contractually fulfill the acquisition need was qualified. Using low cost and unqualified distributors can cause high quality problems, and squandered time and money in the long run. To assist you via the procedure, right here are some things to consider when choosing the best metal casting supplier.
A business that just uses the financial investment spreading procedure will certainly try to sell you on why that procedure is best for your application (Foundry). However suppose using the sand spreading process is best for you and your demands? Rather, look for a distributor that offers a series of casting processes so the ideal choice for YOU is picked
If functioning with a solitary resource for all of your spreading needs is essential to you, the distributor needs to be varied in its capacities. When incorporated with other incorporated capacities, this can help simplify and press the supply base. When choosing the ideal spreading supplier, mindful factor to consider should be provided to high quality, solution, and cost.
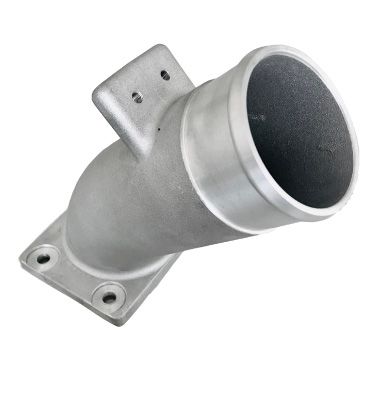
Some Ideas on Premier Aluminum Llc You Need To Know
Purchasers progressively pick casting providers that have machining abilities. If the spreading distributor discovers an issue throughout machining, the problem is dealt with faster with no conflict over whose fault it is.
What do you require from your spreading provider? Are you looking for someone to simply deliver a steel element to your front door or do you require extra?
Others will surpass the letter of the PO to help you conserve time and cash. Do you have requirements for both ferrous and non-ferrous alloys? Some foundries are minimal or specialized. See to it the distributor can meet all your material or alloy requirements to get rid of the need for multiple suppliers.
See This Report about Premier Aluminum Llc
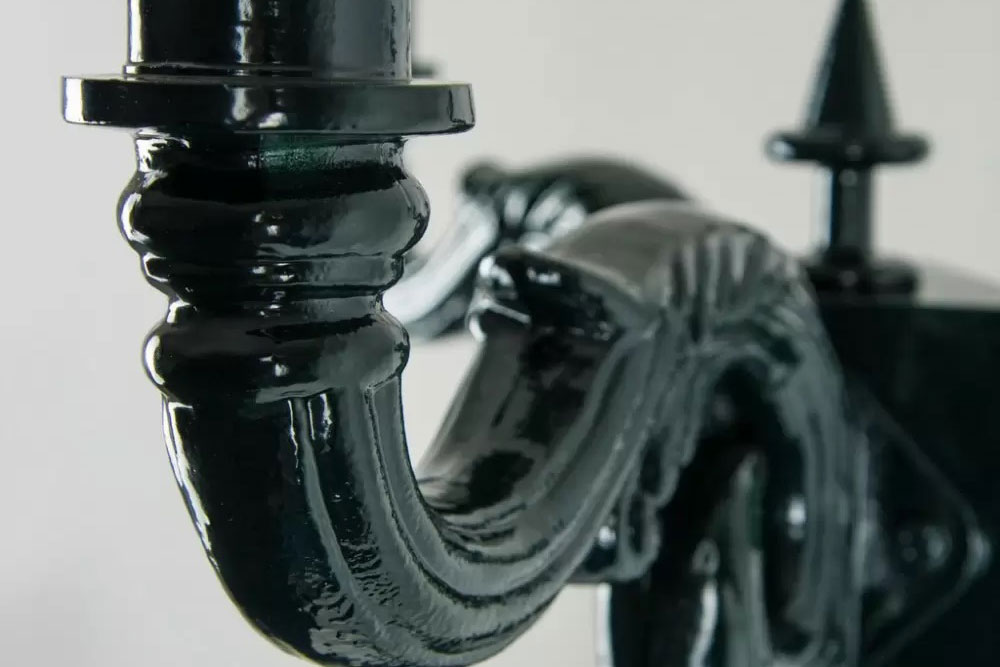
Research the distributor's site. Talk to a sales rep or organization associate.
Light weight aluminum is likewise lightweight and has excellent corrosion resistance, making it excellent for applications where weight and resilience are very important factors. In addition, light weight aluminum casting is a cost-efficient method of production, as it needs much less power and sources than various other methods. Iron casting, on the other hand, includes putting molten iron right into a mold to produce a preferred form.
Getting My Premier Aluminum Llc To Work
Iron spreading is also able to stand up to high temperature levels, making it suitable for use in applications such as engine parts and industrial equipment. Iron casting can be extra pricey than aluminum spreading due to the higher price of raw materials and the power needed to thaw the iron. When deciding in between light weight aluminum spreading and iron casting, it is essential to consider the details needs of the application.
If stamina and toughness are more crucial, iron casting may be the much better alternative. Various other elements to consider include price, production volume, and lead time. In final thought, both aluminum read this casting and iron spreading have their very own special advantages and negative aspects. By meticulously thinking about the particular requirements of the application, makers can choose the ideal process for their product.ZheJiang Dongrun Spreading Industry Carbon Monoxide,. Ltd was built in 1995, We have actually remained in the casting sector for greater than 25 years. Pass away spreading is the name given to the
procedure of producing complex steel components through usage of mold and mildews of the component, also understood as passes away. The process utilizes non-ferrous steels which do not have iron, such as aluminum, zinc and magnesium, because of the desirable residential or commercial properties of the metals such as low weight, higher conductivity, non-magnetic conductivity and resistance to corrosion. Die spreading manufacturing is quickly, making high production degrees of elements simple.
It generates even more components than any type of other procedure, with a high degree of accuracy and repeatability. To find out even more concerning die casting and die spreading materials used in the procedure, read on. There are 3 sub-processes that drop under the category of die casting: gravity pass away casting (or irreversible mold and mildew spreading), low-pressure die spreading and high-pressure die casting. The pure metal, likewise called ingot, is included in the heating system and kept at the molten temperature level of the steel, which is then transferredto the injection chamber and infused into the die. The pressure is then maintained as the metal strengthens. Once the metal strengthens, the cooling process begins. The thicker the wall surface of the component, the longer the cooling time due to the amount of interior metalthat additionally needs to cool down. After the part is totally cooled, the die cuts in half open and an ejection system presses the part out. Complying with the ejection, the die is shut for the following injection cycle. The flash is the added product that is cast throughout the process. This have to be cut off using a trim device to
leave just the major part. Deburring removes the smaller pieces, called burrs, after the cutting procedure. The element is polished, or burnished, to provide it a smooth surface. Nevertheless, this proved to be an incorrect test, due to the fact that the tester can cut into an item and miss out on an area with porosity. Today, top makers use x-ray testing to see the entire interior of elements without reducing right into them. This allows them to much more properly accept or turn down components. To get to the completed product, there are 3 primary alloys utilized as die casting material to pick from: zinc, aluminum and magnesium. Zinc is just one of the most used alloys for die spreading as a result of its lower cost of basic materials.